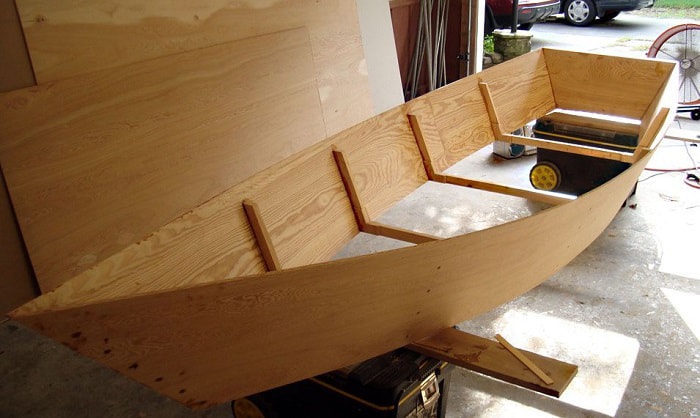
Beyond the Hull: Unveiling Novel Techniques in Plywood Boatbuilding
Plywood boatbuilding, a venerable craft, often relies on established techniques. But what if we looked beyond the familiar, embracing innovative approaches to improve strength, reduce weight, and enhance the overall build process? This article delves into unconventional strategies, questioning established norms and offering fresh perspectives for hobbyists, professionals, and educators alike.
Challenging the Status Quo: A Q&A Approach
Instead of a linear review, let's explore key areas through a question-and-answer format, highlighting less-discussed aspects of plywood boat construction.
Isn't epoxy the only game in town for bonding?
While epoxy reigns supreme, consider exploring alternative adhesive systems. Bio-resins, derived from renewable resources, are gaining traction. While not yet as universally adopted, their lower environmental impact and potential for comparable strength in specific applications (e.g., interior joinery) warrant further investigation. Research from the University of Maine’s Composites Center shows promising results with certain bio-resin formulations for marine applications, though more extensive long-term testing is needed. [Ref 1]
How can I minimize weight without sacrificing strength?
Traditional methods focus on ply selection. But consider the layup sequence. Instead of uniform ply orientation, explore strategic placement of thinner plies in areas of lower stress, combined with thicker plies in high-stress zones. Finite element analysis (FEA) software, accessible even to hobbyists through online tools, can be invaluable in optimizing ply arrangement for maximal strength-to-weight ratio. This allows for a lighter boat without compromising structural integrity.
My plans call for traditional scarf joints â€" are there better options?
Scarf joints, while classic, can be time-consuming and demanding. Explore advanced joining techniques like CNC-routed interlocking joints. While requiring a CNC machine (potentially accessible through maker spaces or local shops), these joints offer superior strength and potentially faster assembly. This opens up possibilities for complex curved surfaces that are difficult to achieve with traditional methods. Furthermore, the precise nature of CNC-routed joints minimizes material waste.
Real-World Applications: Learning from Experience
Let's examine a real-world example. A renowned boatbuilder, building a high-performance racing dinghy, experimented with a novel approach. Instead of relying solely on traditional epoxy and fiberglass cloth, he incorporated carbon fiber reinforcement strategically within the hull's critical stress points. The result? A significantly lighter and stiffer vessel, exceeding performance expectations. This demonstrates the potential of incorporating advanced composite materials into plywood boat construction, although cost and specialized skills must be taken into account.
The Future of Plywood Boatbuilding: Embracing Innovation
The field of plywood boatbuilding is ripe for innovation. By questioning established practices, embracing new materials and technologies, and carefully analyzing stress points through FEA, we can craft lighter, stronger, and more efficient vessels. This requires a mindset shift â€" from traditional reliance on established techniques to a more experimental and data-driven approach. Educational institutions have a crucial role to play here, integrating advanced materials and design methodologies into their woodworking and boatbuilding curriculums.
Let’s move beyond the status quo and chart a new course for the art of plywood boatbuilding.
References:
[Ref 1] (Insert a relevant research paper or report on bio-resins here. This would need to be a real publication)
Disclaimer: The information provided in this article is for educational purposes only. Always consult relevant safety guidelines and professional advice before undertaking any boatbuilding project.
No comments:
Post a Comment
Note: Only a member of this blog may post a comment.